9 Easy Facts About Alcast Company Shown
Table of ContentsThe Alcast Company PDFs6 Easy Facts About Alcast Company DescribedThe Only Guide for Alcast CompanyExcitement About Alcast CompanySome Of Alcast CompanyA Biased View of Alcast Company
Chemical Comparison of Cast Aluminum Alloys Silicon advertises castability by minimizing the alloy's melting temperature and enhancing fluidity during casting. Additionally, silicon adds to the alloy's strength and wear resistance, making it beneficial in applications where sturdiness is essential, such as vehicle parts and engine elements.It additionally enhances the machinability of the alloy, making it much easier to refine right into ended up items. In this method, iron contributes to the general workability of aluminum alloys.
Manganese adds to the strength of light weight aluminum alloys and improves workability (Foundry). It is generally utilized in wrought aluminum products like sheets, extrusions, and profiles. The existence of manganese aids in the alloy's formability and resistance to cracking throughout fabrication procedures. Magnesium is a light-weight component that offers stamina and impact resistance to light weight aluminum alloys.
Some Known Details About Alcast Company
Zinc enhances the castability of aluminum alloys and assists control the solidification procedure during casting. It improves the alloy's toughness and firmness.
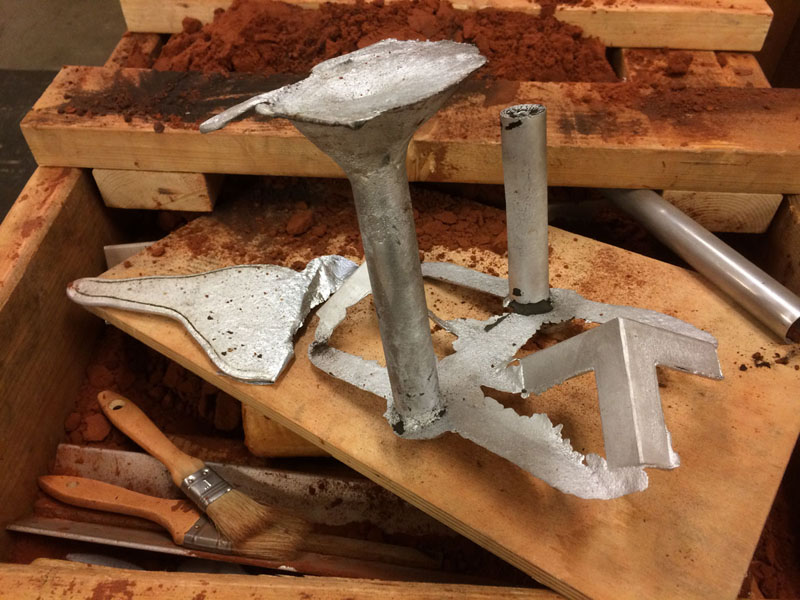
The primary thermal conductivity, tensile toughness, yield toughness, and elongation vary. Select suitable resources according to the performance of the target product generated. Amongst the above alloys, A356 has the highest possible thermal conductivity, and A380 and ADC12 have the most affordable. The tensile restriction is the contrary. A360 has the ideal return strength and the greatest elongation rate.
Alcast Company Things To Know Before You Get This

Its unique residential properties make A360 a valuable selection for precision spreading in these sectors, improving product durability and quality. Foundry. Light weight aluminum alloy 380, or A380, is an extensively used casting alloy with several distinctive attributes.
In precision spreading, aluminum 413 shines in the Customer Electronic Devices and Power Tools markets. It's typically used to craft detailed elements like smart device housings, cam bodies, and power tool cases. Its precision is impressive, with tight resistances up to 0.01 mm, making sure perfect item assembly. This alloy's superior corrosion resistance makes it an excellent option for exterior applications, making sure resilient, durable products in the mentioned industries.
Facts About Alcast Company Uncovered
The light weight aluminum alloy you choose will considerably affect both the spreading process and the buildings of the last product. Because of this, you need to make your decision carefully and take an educated technique.
Establishing More Help the most ideal light weight aluminum alloy for your application will certainly suggest evaluating a vast array of features. These relative alloy qualities follow the North American Die Casting Organization's standards, and we've separated them into two categories. The very first classification addresses alloy attributes that influence the manufacturing procedure. The second covers attributes impacting the homes of the last product.
How Alcast Company can Save You Time, Stress, and Money.
The alloy you choose for die spreading directly affects several aspects of the casting process, like just how simple the alloy is to deal with and if it is vulnerable to casting defects. Hot splitting, likewise called solidification cracking, is a common die spreading defect for light weight aluminum alloys that can result in interior or surface-level tears or cracks.
Specific light weight aluminum alloys are more vulnerable to warm breaking than others, and your option should consider this. It can damage both the cast and the die, so you need to look for alloys with high anti-soldering homes.
Corrosion resistance, which is currently a noteworthy feature of light weight aluminum, can vary considerably from alloy to alloy and is a necessary particular to consider relying on the environmental conditions your item will certainly be revealed to (Foundry). Wear resistance is one more building commonly looked for in light weight aluminum items and can distinguish some alloys